Recently, during my travels, I encountered an unexpected flight delay at Amsterdam airport that shed light on a significant issue: preventable profit margin waste. The scene was all too familiar – interminable queues at check-in counters, exacerbated by a glaring shortage of personnel. As a consequence, I, along with numerous fellow passengers, missed our flights. This setback led to a frustrating 10-hour wait before rebooking for the following day and prompted my contemplation about the avoidable loss incurred by the airline.
Amidst the collective inconvenience, it struck me that had effective measures been in place to prevent profit margin waste; the airline could have reaped substantial benefits. By optimizing operational efficiency, not only could the original flight have taken off with a full complement of passengers, but the replacement flight could have accommodated additional travelers, bolstering profits in the process.
This experience made me see how easily a company can lose profit and reminded me of a book I read long ago called Six Sigma Simplified by Jay Arthur. This book talks about a tale of two factories.
According to Jay Arthur, every business has two “factories” running simultaneously:
- The “Good Factory” is where you focus most of your energy on producing goods and services for your customers.
- The “Fix-it Factory” cleans up all of the mistakes, rework, defects, breakage, returns, scrap, and other problems of the “Good Factory.”
The “Fix-it Factory,” in most cases, is overlooked. This is where frustrations accumulate and also the area where valuable resources such as time, energy, and clients are lost. As a business owner, the “Fix-it Factory” can prevent you from sleeping at night and give you grey hairs prematurely.
In other words, the “Fix-it Factory” consumes the company resources without any positive output. The cost of running a “Fix-it Factory” in any business is enormous and very harmful. Let’s illustrate the effects of the “Fix-it Factory” on the company using the following example.
Jay Arthur says the “Fix-it Factory” costs 25 to 40% of every 100 Euros you spend. That means, for 100,000 Euros paid, a company could have saved 25,000 to 40,000 Euros; or for 500,000 Euros spent, they could have saved 125,000 to 200,000 Euros, and the saving could have reached 250,000 to 400,000 Euros for 1,000 000 Euros spent.
The “Fix-it Factory” cost is even higher because you don’t pay it out of the revenue but directly out of the company’s bottom line.
Let’s consider a company with one-million Euros in sales. Let’s assume they have only 3% waste. That means the “Fix-it Factory” will cost them 30,000 Euros. Considering this company has an 8% net profit before taxes, their profit will be only 80,000 Euros – 30,000 Euros = 50,000 Euros.
The pain is even more significant when you consider that to get to the same profit level, the company has to sell nearly 400,000 Euros more to make up for this 30,000 Euros loss. Just imagine if the business can save a fraction of the money used by the “Fix it Factory.”
Why do we have the “Fix it Factory” in the first place?
When you look closely at the origin of the elements that compose a “Fix-it Factory,” you will note that they primarily deal with human-related errors. In most cases, it has something to do with negligence or ignorance. The waste could be avoided at some point, but the concerned people failed to see it and take action. Whether machine or material driven, the error can always be attributed to human-related errors.
As a business owner, you have probably experienced the following situation. You walk through your company and see signs of waste here and there, plain as day, and yet no one has noticed them. You wonder, “How come they are not seeing them?”
The business owner should not be the only one fighting to reduce wastage and maximize profits. Every team member should take part in helping to ensure the “Fix it Factory” is not active. This can allow the owner to focus on other things that benefit the company. A busy “Fix it Factory” can be draining to the business owner, considering he cannot take time off the company without expecting a disaster when they return. The “Fix it Factory” takes away the entrepreneur’s dream of independence and freedom.
How do you prevent having a “Fix-it Factory”?
- Get the right people on board and train them properly
- Create a culture where people are aware of the process
- Create systems that can easily detect the wastes and eradicate them
- Do daily exercises with your personnel to get them to be in the now
- Make a list of the elements of the “Fix-it Factory” of your company and get everyone aware of them and how to prevent them
- Value the “Good Factory” more and give it more attention than the “Fix-it Factory.”
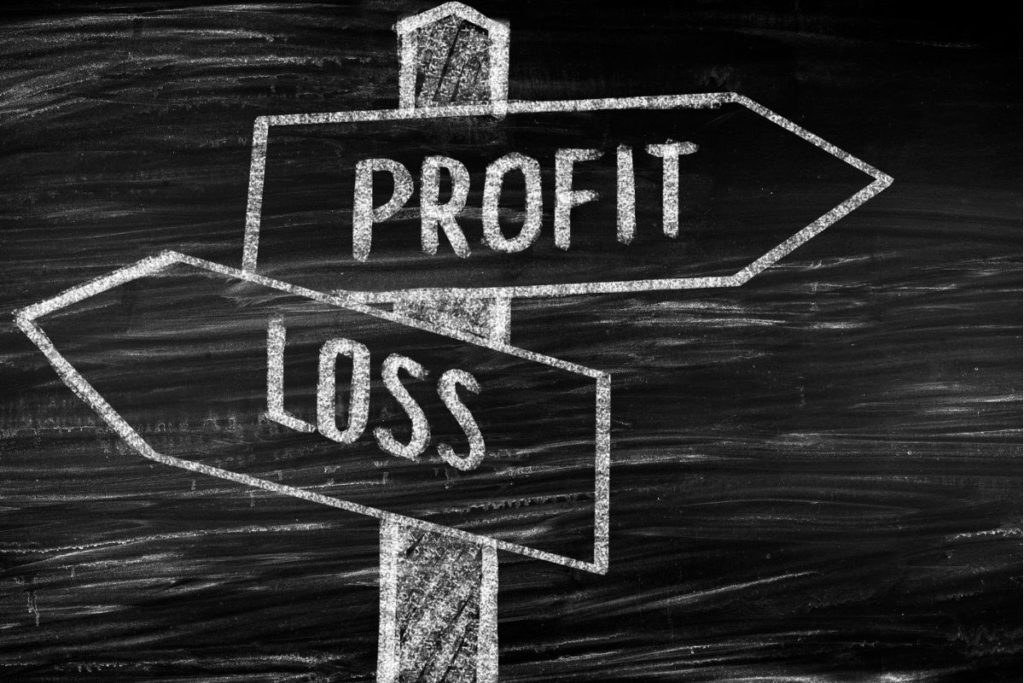
Conclusion
I hope this article has brought to your awareness the concept of “Fix-it Factory” and how this can negatively affect your “Good Factory.” Take some time to evaluate your company to determine the places, size, and cost of what is feeding your “Fix-it Factory.” Then find a way to eliminate them.
Join the conversation by sharing your experience with us, and if you need help fixing it, we will gladly help.